Los refrigerantes son elementos básicos para que cualquier equipo HVACR funcione adecuadamente, por lo tanto, aprender a gestionarlos, reciclarlos, recuperarlos y regenerarlos es fundamental para la labor de un técnico.
Carlos González Sierra / Imágenes: cortesía del autor
Los hidrocarburos halogenados son elementos muy comunes en la industria del aire acondicionado y la refrigeración; sin embargo, su aplicación contribuye al calentamiento de la atmósfera. Al mismo tiempo, los compuestos que contienen cloro y/o bromo tienen un alto poder destructivo del ozono estratosférico. Esto ha obligado a que gran parte de estas sustancias hayan sido reguladas por el Protocolo de Montreal (sustancias que agotan la capa de ozono) y el Protocolo de Kioto (Gases de Efecto Invernadero o GEI).
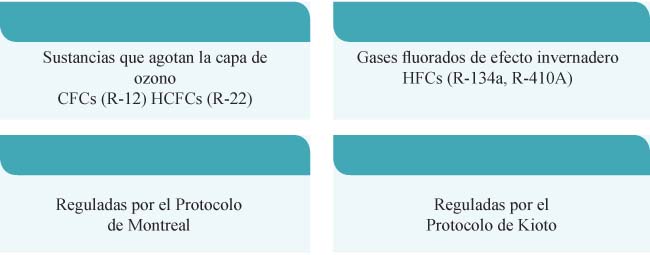
Figura 1. Protocolos de Montreal y Kioto
Cambio climático y Protocolo de Montreal
Una parte de la energía emitida por el Sol es reflejada por la atmósfera terrestre; el resto llega a la Tierra, en donde produce el calentamiento de la misma. El calor emitido hacia el espacio sideral en forma de rayos infrarrojos queda atrapado en la atmósfera impidiendo su salida. A este fenómeno se le conoce como “efecto invernadero”, el cual se ve agravado por el tiempo de permanencia de los gases en el espacio atmosférico. Por ejemplo, el bióxido de carbono (CO2) permanece en éste unos 500 años. Es lo que se llama tiempo estimado de vida para cada gas. Mientras mayor sea el tiempo de vida estimado de un refrigerante, mayor será su potencial de efecto invernadero.
En el segmento de la refrigeración, una instalación que trabaje con baja eficiencia contribuye a potenciar el efecto invernadero, aunque no tenga fugas de refrigerante. Esto es debido a que la baja eficiencia significa un mayor consumo de energía y, en consecuencia, mayores emisiones de CO2 por parte de las plantas generadoras de electricidad. Por esta razón, además de mantener controladas las emisiones en las instalaciones, éstas deben trabajar con la más alta eficiencia.
El Protocolo de Kioto (diciembre de 1997) complementa y amplía el de Montreal, promocionando la investigación, desarrollo y aumento del uso de nuevas formas de energías renovables y de tecnologías de secuestro del CO2, comprometiendo a los países firmantes a bajar sus emisiones expresadas en dióxido de carbono equivalente de GEI.
El Potencial de Calentamiento Atmosférico (PCA) o Global Warming Potencial (GWP) es el parámetro que mide el potencial de elevación de la temperatura producido por 1 kilogramo (kg) de toda sustancia emitida a la atmósfera, en relación con el efecto producido por 1 kg CO2, que se toma como referencia sobre un periodo de integración dado. Cuando el tiempo de integración es de 100 años se indica con PCA 100.
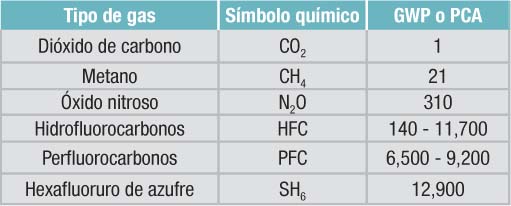
Tabla 1. Potencial de Calentamiento Atmosférico
Impacto del TEWI
El Total Equivalente del Impacto Total en el Calentamiento (TEWI, por sus siglas en inglés) es un parámetro utilizado para evaluar el calentamiento atmosférico producido durante el tiempo de funcionamiento de un sistema de refrigeración. Esto más la contribución directa de las emisiones del refrigerante hacia la atmósfera y la contribución indirecta de las emisiones de CO2, las cuales son resultado del consumo energético del sistema de refrigeración durante su periodo de vida útil.
El TEWI ha sido concebido para determinar la contribución total del sistema de refrigeración utilizado al PCA. También cuantifica el calentamiento atmosférico directo del refrigerante si se libera, así como la contribución indirecta de la energía requerida para que el equipo trabaje durante su vida útil. Es válido únicamente para comparar sistemas alternativos u opciones de refrigerantes en una aplicación concreta y en un lugar determinado.
Para un sistema frigorífico determinado, el TEWI incluye:
- El impacto directo sobre el PCA bajo ciertas condiciones de pérdida de refrigerante
- El impacto directo sobre el PCA por los gases emitidos por el aislamiento u otros componentes, si procede
- El impacto indirecto sobre el PCA por el CO2 emitido durante la generación de la energía consumida por el sistema
El factor TEWI puede calcularse por medio de la siguiente fórmula, en la que los diferentes tipos de impacto están correspondientemente separados.
TEWI- [PCA·L·n] + [PCA·m· (1-αrecuperación)] + [n·Eanual· β]
[PCA·L·n] = Impacto debido a pérdidas por fugas = PCAdirecto
[PCA·m·(1-αrecuperación)] = Impacto por pérdidas producidas en la recuperación = PCAdirecto
[n · Eanual· ]= Impacto debido a la energía consumida = PCAindirecto
En donde:
TEWI = contribución total por el efecto invernadero (kg de CO2)
PCA = potencial de efecto invernadero global (referido a CO2)
L = fugas (kg/año)
n = tiempo de funcionamiento del sistema (años)
m = carga de refrigerante (kg)
αrecuperación = factor de recuperación (de 0 a 1)
Eanual = consumo energético (kWh/año)
β = emisión de CO2 (kg×kWh)
Este potencial de calentamiento atmosférico está determinado respecto del CO2 y se basa en un horizonte de tiempo de integración acordado de 100 años. A su vez, el factor de conversión expresa la cantidad de CO2 producido por la generación de 1 kWh.
Ultravioleta A (UV-A). Longitud de onda entre 315 a 400 nm. Los efectos sobre las personas son similares a los de la UV-B, pero con dosis 1 mil veces superiores, por lo que proporcionalmente resulta menos perjudicial, aunque la intensidad que alcanza en la superficie terrestre es muy superior a la UV-B.
Ultravioleta B (UV-B). Longitud de onda entre 280 y 315 nm. Parte de esta radiación es absorbida por el ozono, pero el 10 % alcanza la superficie terrestre y afecta a los seres vivos. Además del bronceado, sus efectos sobre las personas son: quemaduras, envejecimiento de la piel, cáncer de piel, conjuntivitis, etcétera.
Ultravioleta C (UV-C). Longitud de onda entre 100 y 280 nm. Es altamente dañina para los seres vivos y en presencia de la cual no sería posible la vida en la Tierra. Esta radiación es totalmente absorbida por el ozono estratosférico, vapor de agua y gases (O2, CO2), de modo que en ningún caso alcanza la superficie terrestre.
Agotamiento de la capa de ozono
Los hidrocarburos halogenados, además de contribuir al calentamiento de la atmósfera, presentan un alto poder destructivo del ozono estratosférico, lo que ha obligado a que estas sustancias se regulen por el Protocolo de Montreal (septiembre de 1987).
La radiación solar ultravioleta es parte del espectro electromagnético emitido por el Sol, y de acuerdo con su longitud de onda es clasificada en tres tipos (ver figura 2): A, B Y C.
El ozono (O3) es una sustancia que constituye un filtro natural de la radiación solar ultravioleta (UV). De esta forma, al absorberla en las capas altas de la atmósfera, se evita que llegue a la superficie terrestre, permitiendo el desarrollo de las diferentes formas de vida. El O3 se forma en la estratosfera por la incidencia de los rayos UV del Sol sobre las moléculas de oxígeno (O2), descomponiéndolas y formando dos átomos de oxígeno:
O2 + UV O + O (1)
Uno de los átomos de O se une a una molécula de O2 formando el ozono (O3):
O2 + O O3 (2)
En 1974, dos investigadores de la Universidad de California, Mario Molina y Sherwood Rowland (ganadores del Premio Nobel de Química 1995), formularon la Teoría del Ciclo Catalítico del Cloro (Teoría química de la destrucción de la capa de ozono). Sus estudios de laboratorio demostraron que los CFC son poco estables ante la radiación UV-C, pues se produce una reacción fotoquímica que da lugar a la liberación de átomos de cloro (Cl):
Cl3CF (R-12) + UV Cl2CF + Cl (3)
Los átomos de cloro que se liberan son muy reactivos y muchos de ellos colisionan con moléculas de ozono produciendo monóxido de cloro (ClO) y oxígeno molecular:
Cl + O3 ClO + O2 (4)
Pero aquí no termina todo. El monóxido de cloro puede reaccionar con átomos de oxígeno producidos en la reacción (1), y se regenera así el cloro atómico:
ClO + O O2 + Cl (5)
Se estima que un solo átomo de cloro liberado de un CFC puede dar origen a una reacción en cadena que destruya 100 mil moléculas de ozono.
Para determinar en qué medida los diferentes gases refrigerantes influyen en este proceso se utiliza un indicador: el Potencial de Destrucción del Ozono (ODP), el cual indica la cantidad destruida por la emisión de un determinado refrigerante. Este índice toma como referencia el efecto que produce el R-11. Por tanto, al R-11 se le asigna un ODP de 1.
Recuperación, reciclado y regeneración
Las normas de muchos países prohíben a los técnicos dejar escapar conscientemente los refrigerantes al medioambiente. Estas normas suelen excluir de la prohibición las pérdidas mínimas que necesariamente se producen con cualquier intento bien intencionado de recuperar, reciclar o eliminar de forma segura dichas sustancias.
Recuperación
Es el proceso de extraer refrigerante de un sistema y almacenarlo en un envase externo, sin procesarlo. La sustancia puede estar contaminada con aire, otro refrigerante, nitrógeno, ácido, agua o partículas generadas al quemarse un motor.
Un refrigerante recuperado no debe ser empleado en otro sistema a menos que se esté seguro de que está limpio. Si se ha extraído del mismo y éste funciona puede cargarse de nuevo. Este es el caso de un sistema en el que se produce una fuga y no tiene válvulas de servicio.
Cabe recordar que el refrigerante no puede venderse a otro cliente sin antes asegurarse de su limpieza, según las normas existentes.
Reciclado
Es el proceso de limpiar el refrigerante con ayuda de una recicladora, separando el aceite y realizando uno o más pasadas a través de dispositivos, como los filtros, que reduzcan la humedad, la acidez y la presencia de partículas contaminantes. El reciclado suele implicar su reinstalación en el aparato, que con frecuencia se produce in situ.
Regeneración
Consiste en procesar refrigerante con el fin de alcanzar un rendimiento equivalente al de una sustancia virgen. La regeneración incluye los procedimientos de filtrado, secado, destilación y tratamiento químico, lo que implica el tratamiento en un lugar distinto al de la instalación (planta de regeneración o reprocesamiento). La sustancia recuperada se almacena en botellas normalizadas y se transporta a la planta de regeneración, donde es analizada químicamente para determinar si puede ser regenerada o no.
Tipos de recuperación
La recuperación se puede realizar de dos maneras:
1. En el propio equipo
Su finalidad es recuperar todo el refrigerante en una parte del circuito (unidad exterior, condensadora o depósito de líquido). Para llevarla a cabo, se necesita por lo menos una válvula o llave de servicio que corte el paso de la sustancia. Se cierra el paso de la válvula con el equipo en marcha, por lo que el compresor vaciará de refrigerante la instalación almacenándolo en la zona prevista. El proceso se da por terminado cuando la presión del manómetro se aproxime a la lectura de 0 bar, desconectando entonces la alimentación del equipo.
2. En un recipiente de recuperación
El refrigerante puede extraerse en forma de vapor o de líquido, o en el estado parcialmente líquido y de vapor. En el sistema circula también aceite lubricante, por lo que si se extrae en estado gaseoso, es más probable que el aceite permanezca en el circuito. Esto resulta deseable por dos razones:
- Si el aceite está contaminado, puede que sea necesario manejarlo como residuo tóxico. En estos casos, es fundamental adoptar muchas más precauciones y debe estar disponible un técnico con certificación para manejo de residuos tóxicos
- Si el aceite permanece en el sistema, no será necesario medirlo y volverlo a introducir, lo que ahorrará tiempo y dinero. El técnico debe prestar una cuidadosa atención al manejo del aceite de cualquier sistema
Cabe destacar que los refrigerantes sólo deben transferirse a botellas normalizadas, la cuales son reconocibles por su color y tipo de válvula. Suelen tener una parte superior de color amarillo o verde, el cuerpo gris y una válvula especial que permite añadir o extraer líquido o vapor de las mismas. La botella debe estar limpia y en un vacío profundo antes de iniciar el proceso de recuperación o reciclado.
Técnicas de recuperación
De acuerdo con el Manual de buenas prácticas en sistemas de refrigeración y aire acondicionado de la Secretaría de Medio Ambiente y Recursos Naturales (Semarnat) del ingeniero Gildardo Yañez, las dos técnicas de recuperación son:
A. En fase gaseosa
Por lo general, este procedimiento es el más lento, ya que el flujo de gas refrigerante es menor en fase gaseosa. En los grandes sistemas de refrigeración esto exige más tiempo que cuando se transfiere líquido.
Es necesario tener presente que las mangueras de conexión entre la máquina recuperadora, el sistema de refrigeración y la botella de recuperación deben ser de la longitud mínima posible, así como del diámetro interior máximo posible, con la finalidad de contribuir a aumentar el rendimiento del proceso. El refrigerante, en fase de vapor, es normalmente absorbido por la aspiración de la máquina recuperadora y, una vez condensado, es enviado a la botella de recuperación como se muestra en la figura 3.
B. En fase líquida
Debido a que los compresores sólo pueden trabajar con refrigerante en fase gaseosa, es necesario evaporarlo todo y extraerlo del sistema antes de que llegue al compresor. Para ello, es necesario agregarle calor, lo cual debe hacerse mediante prácticas seguras.
El refrigerante líquido puede ser recuperado mediante técnicas de decantación, separación o push/pull (succión y retroalimentación), con el consiguiente arrastre de aceite.
Las operaciones de recuperación con el método push/pull se llevan a cabo usando vapor de la botella para empujar el refrigerante líquido fuera del sistema. Se conecta una manguera desde la válvula de mantenimiento de líquido (en este caso, una unidad de climatización), cuyo refrigerante se busque extraer a la válvula de líquido de la botella de recuperación. Posteriormente, se conecta otra manguera desde la válvula de vapor de la botella de recuperación a la entrada de la succión de la máquina recuperadora y, finalmente, se conecta una tercera manguera desde la salida o la descarga de la máquina recuperadora hacia la válvula de mantenimiento de vapor del equipo, como se muestra en la figura 4.
De esta manera, la botella de recuperación succionará el refrigerante líquido (movimiento pull) de la unidad de climatización desactivada, cuando la máquina recuperadora haga disminuir la presión de la botella. El vapor succionado por la máquina recuperadora será entonces empujado de vuelta (movimiento push), es decir, comprimido hacia el lado que corresponde al vapor en la unidad de climatización desactivada.
Una vez que la mayoría del refrigerante haya sido cargado del sistema a la botella de recuperación, la maquina recuperadora comenzará a ciclar, controlada por su presostato de baja presión de succión, removiendo el resto del refrigerante en forma de vapor. Cuando la máquina de recuperación ya no continúe ciclando y se detenga por completo, esto indicará que se ha recuperado todo el refrigerante posible del sistema.
Finalmente, es importante recordar que el proceso de recuperación debe implementarse siguiendo las buenas prácticas, para evitar emisiones al medioambiente o situaciones que pongan en riesgo la vida del técnico y de las personas. Por ello, el técnico encargado de realizarlo deberá asegurarse de que el trabajo se realice con seguridad y conocimiento.
Carlos González Sierra. Ingeniero de Estructuras e Instalaciones Industriales y Maestro en Refrigeración y Acondicionamiento de Aire. Cuenta con un postgrado en Energías Renovables y Procesos de Ahorro Energético por la Universidad Politécnica de Cataluña (UPC). Autor de ocho libros de refrigeración y climatización. Actualmente es coordinador de Educación Continua 2017-2018 de ASHRAE Capítulo Monterrey y director de Ingeniería en SENSA.