Podemos identificar varios cambios en nuestro entorno sucedidos a través del tiempo; la mayoría de éstos se presentan en avances tecnológicos derivados de un mayor conocimiento científico, entre ellos la evolución de los compresores digitales
Víctor Galván / Imágenes: cortesía de Emerson
Actualmente, los procesos alimenticios o de conservación deben de cumplir ciertas condiciones que permitan salvaguardar la calidad de los productos. A continuación, identificaremos cómo estas actualizaciones marcan una tendencia en la refrigeración, específicamente, dentro de compresores con tecnología digital. Asimismo, entenderemos su aplicación, ventajas y algunas otras cuestiones relacionadas con su implementación.
Recordemos que un sistema de refrigeración es un circuito idealmente hermético que permite mantener una temperatura menor a la del ambiente, dependiendo de la aplicación de uso. Estos sistemas requieren como mínimo cuatro componentes principales para su operación: evaporador, condensador, válvula de expansión y compresor. Si bien los cuatro componentes son indispensables para el circuito, hacer una correcta selección del compresor incrementa la eficiencia del proceso de forma considerable. Copeland Discus™ cuenta con tecnología única que permite mayor eficiencia y capacidad que otros compresores convencionales. Esta capacidad es atribuida a su diseño de plato de válvulas, el cual favorece que el ciento por ciento del cabezal opere con presión de descarga en comparación con otros compresores. Esto evita que de manera interna se tenga una re-expansión que aumente la eficiencia volumétrica del compresor. Además, estos compresores están acondicionados para trabajar con múltiples refrigerantes minimizando las caídas de presión.
Dentro de los compresores existe la posibilidad de modular la capacidad. Esta modulación posibilita variar la operación para lograr una mayor eficiencia en el tiempo de funcionamiento cuando se requieren cargas más ligeras en el sistema; en otras palabras, nos permite mantener una temperatura más exacta para procesos críticos de enfriamiento. La necesidad de mantener un rango ideal de operación conlleva el uso de un compresor con modulación. Esto porque existen diferentes condiciones que alteran la operación de un sistema de refrigeración y estas variables no pueden ser cien por ciento controlables, a saber: condiciones ambientales o tiempos de intercambio de calor en vitrinas expuestas a usuarios finales.
Compresores Discus™ y la modulación
La modulación de compresores Discus™ puede ser clasificada por descargadores o tecnología digital y el tipo de modulación dependerá del número de cabezales que se tengan en el compresor. La modulación digital nos permite tener un control infinito de 10 a 100 por ciento en aplicaciones de media temperatura, a diferencia de aplicaciones de baja temperatura que nos limita a un control de un 30 a un 100 por ciento, recordando que requerimos un mayor flujo másico para evitar sobrecalentamientos en el compresor.
La modulación digital la podemos identificar en compresores Copeland Scroll o compresores Copeland Discus™ reciprocantes. En el caso de los compresores Scroll, esta ingeniería acciona un bypass del lado de alta presión y genera una separación mínima entre las espirales evitando la compresión (Figura 1). En cambio, en los compresores reciprocantes se activa una válvula solenoide, misma que bloquea los puertos de succión para evitar el paso de gas refrigerante.
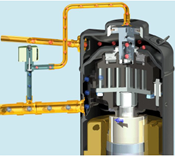
Figura 1. Compresor Scroll digital
Es muy importante considerar que la velocidad operacional del compresor no se ve alterada por esta tecnología, lo que nos permite mantener una velocidad constante y, con ello, un flujo de aceite necesario para evitar fallas por falta de lubricación en componentes mecánicos.
A diferencia de la modulación digital, los descargadores sólo permiten tener un control por medio de succión bloqueada en los cabezales, aplicado solamente en compresores reciprocantes y mayores a dos cabezas, lo que nos limita a tener un control finito. Es posible combinar ambos tipos de modulación siempre y cuando tengamos un compresor mayor a dos cabezales, considerando que dentro de las instalaciones sólo se puede colocar un compresor digital por grupo de succión, el cual soportará las variaciones de carga.
¿Por qué la modulación digital amplía la vida útil de los compresores?
La vida útil de un compresor depende de condiciones ambientales, instalaciones apropiadas y mantenimientos. Sin embargo, hay que considerar que el factor operacional es de suma importancia para identificar el número de ciclos de un compresor. Entre más números de paros y arranques tengamos, la vida útil del compresor se verá deteriorada. A esto hay que sumarle el aumento en consumo eléctrico derivado de los picos de corriente.
En la Figura 2 podemos observar cómo se comparte un sistema con tres compresores. Si visualizamos en la parte superior del gráfico, podemos identificar cómo es la operación del compresor número 1. Cuando es un compresor digital no se apagará durante la operación del sistema con la finalidad de ajustarse a las cargas más ligeras de operación, a diferencia de un compresor convencional (parte central del gráfico), muestra un ciclado excesivo para adaptarse a las condiciones de trabajo.
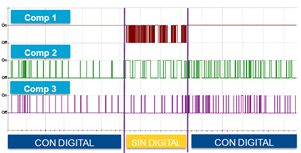
Figura 2. Comparación on/off compresores digitales versus compresores convencionales
¿Qué beneficios ofrecen los compresores digitales en la calidad de los productos?
Para la cadena de frío es de suma importancia mantener las temperaturas de los productos. Cuando éstas no se realizan de manera correcta estos procedimientos de conservación o congelación, los productos pueden llegar a mermar de manera considerable e incluso de forma irreversible. Existe una relación directa entre la presión de succión y la temperatura del cuarto frío y es ahí donde los compresores digitales tienen su mayor aportación.
En la Figura 3 identificamos que la modulación digital permite un control más preciso de temperatura, ya que el compresor gradúa su operación para ajustarse a la demanda del sistema. Caso contrario al de un compresor convencional, que tendrá un excedente de ciclos para tratar de graduar la temperatura; sin embargo, éste alcanzará un diferencial del 30 al 40 por ciento en presión, pues su operación será del 0, o bien, del 100 por ciento.
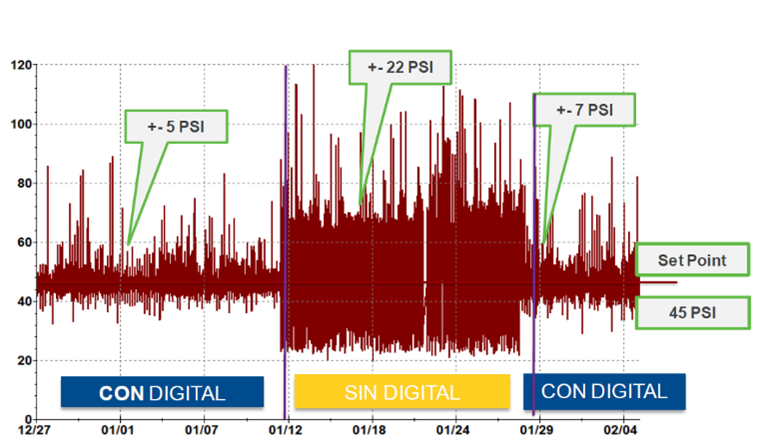
Figura 3. Presión de succión, temperatura de cuarto – tiempo
En cuanto al tema de control es importante identificar qué tipo de compresor tenemos en nuestra instalación, ya que los compresores scroll digitales pueden ser modulados mediante Coresense Diagnostics. A diferencia de los compresores Discus™, los cuales deben ser instrumentados por un control IDCM, termistor de descarga y, para ambos casos, la bobina que energiza la válvula solenoide. La función del control IDCM es convertir la salida analógica de nuestro control principal a una salida de voltaje a pulsos de 20 segundos, con los cuales lograremos la modulación correspondiente.
En conclusión, podemos decir que los compresores digitales muestran beneficios considerables a comparación de los equipos convencionales, por lo que es de suma importancia que sean considerados en la fabricación o modificaciones de los sistemas, trayendo beneficios en calidad de productos a las empresas.
Victor Galván
Ingeniero mecánico por el Instituto Politécnico Nacional. Cuenta con 5 años de experiencia en aire acondicionado y refrigeración. Actualmente, se desempeña como ingeniero de Aplicaciones en Emerson de México enfocado en soporte técnico, garantías y capacitaciones.