El Estándar ASHRAE 52.2 ofrece un método para probar la eficiencia en la remoción de partículas conforme a su tamaño, por parte de los dispositivos purificadores de aire (filtros) para ventilación general
Fernando Bonilla / Gráficas y esquemas: cortesía del autor
Los métodos de prueba de filtros fueron desarrollados conforme la situación (social/laboral) y el paso del tiempo lo fueron demandando. La protección a los equipos y serpentines fue el primer objetivo, después la reducción de los residuos “descargados”. El primer Estándar que ASHRAE creó y utilizó en la evaluación de filtros para aire fue el 52.1, el cual se basa en el peso de los contaminantes y no en el tamaño de la partícula.
Ahora, el requerimiento es la calidad ambiental interior, las partículas respirables, la protección de productos durante el proceso de manufactura, etcétera. Es decir, debemos considerar el tamaño de las partículas.
¿Qué es el Estándar 52.2?
Es el compendio de todos los elementos necesarios para evaluar los filtros de aire, a fin de determinar un valor que permita comparar el desempeño en función de la eficiencia; esto para remover partículas, según su tamaño, de la corriente de aire que lo atraviesa. Se diseñó para comparar filtros con un nivel uniforme de rendimiento (condiciones estandarizadas de operación).
Establece una descripción del método de prueba en laboratorio, especificaciones de desempeño para los dispositivos requeridos para las pruebas, métodos de cálculo y reporte de resultados, además de fijar un valor de eficiencia mínima que puede ser aplicado a los dispositivos purificadores.
Para ello, es importante considerar los siguientes conceptos:
Downstream / upstream. Cuando se habla de filtros, siempre se dice que el lado de alta presión es la entrada del aire al filtro. Esto se debe a que el filtro opone resistencia al paso del aire, por lo que ahí se ejerce mayor presión sobre el mismo. Ése sería el lado de alta presión, mientras que la salida del filtro sería el de baja presión. También se puede explicar como entrada y salida de aire del filtro: upstream, entrada, y downstream, salida.
Área de paso. La zona total del filtro que se expone al flujo de aire se mide en metros (o pies) cuadrados, en un plano perpendicular al eje del ducto de prueba. Todas las pestañas o rebordes internos son parte del área; sin embargo, los accesorios para montar el dispositivo o cableado no se incluyen.
Velocidad de paso. El flujo de aire sobre el área del filtro expresada en metros/segundo (pies por minuto).
Resistencia final. La resistencia al flujo de aire que presenta el filtro sobre el cual han sido realizadas las pruebas y calculados los resultados se mide en Pascales (Pa) o Pulgadas Columna de Agua (PCA).
Resistencia inicial. Pérdida de presión que experimenta el filtro mientras opera con un flujo de aire determinado, sin carga de partículas. Se mide en Pa o PCA.
Media. Agente que se encarga de la eliminación o retención del contaminante (polvo, gas, etcétera).
Resistencia final medida. Relación entre la pérdida de presión operacional y el flujo de aire que expresa en qué momento un dispositivo debe ser sujeto a mantenimiento, o ser reemplazado (según recomendaciones del fabricante). La resistencia final se expresa en Pa o PCA.
MERV. Valor de la Eficiencia Mínima Reportado para un filtro.
Instrumentos de prueba
Los tamaños, dimensiones y arreglos clave de los instrumentos de prueba se muestran en esta sección y en la Sección 5 del estándar. Todos los tamaños descritos son obligatorios a menos que se indique lo contrario:
- Ducto de prueba
- Fuente de aire para la prueba
- Aerosol de prueba
- Contador(es) de partículas
- Instrumento de prueba para la
- carga de polvo
Instrumentos de calificación de pruebas
Los instrumentos para calificar las pruebas deberán verificar cuantitativamente que el tren de prueba y los procedimientos de muestreo tengan la capacidad de proveer medidas eficientes. Las pruebas de calificación se realizarán para:
- Uniformidad en la velocidad del aire en el ducto de prueba
- Uniformidad en el aerosol en el ducto de prueba
- Mezcla de aerosol en el flujo de descarga
- Pruebas de sobrecarga en el contador de partículas
- Prueba del 100 % de eficiencia
- Prueba de tasa de correlación
- Tiempo de respuesta del generador de aerosol
- Pruebas de fugas en el ducto
- Contador de partículas cero
- Precisión del contador de partículas (al medir tamaño)
- Radioactividad del neutralizador
- Tasa de flujo de aire del cargador de polvo
- Eficiencia del filtro final
A continuación, se muestra un ejemplo de las “variaciones” en la precisión de los instrumentos de calificación permitidas:
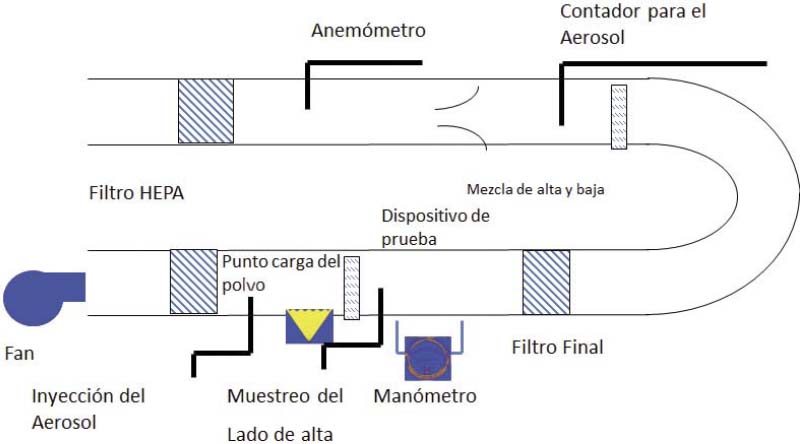
Uniformidad en la velocidad del aire en el ducto de prueba
Basado en la velocidad de cruce por una retícula de 9 puntos de igual área, se permite un coeficiente de variación (CV) menor al 10 por ciento:
Los instrumentos para calificar las pruebas deberán calibrarse periódicamente. Los certificados correspondientes son parte integral de la documentación de las pruebas efectuadas.
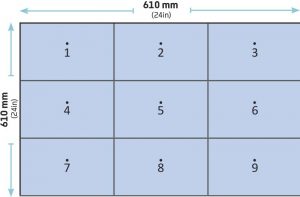
En cuanto a los materiales de prueba, se deben considerar los siguientes:
Aerosol de prueba: partículas de cloruro de potasio (KCl) en fase sólida generadas a partir de una solución acuosa.
Polvo de carga: éste es idéntico al polvo que se encuentra comercialmente disponible para realizar pruebas de ANSI / ASHRAE estándar 52.1-1992.
Filtro final: captura cualquier remanente del polvo de prueba que penetre el filtro durante el procedimiento de carga de polvo.
Selección y preparación de las pruebas
La muestra deberá seleccionarse de un grupo de seis o más filtros tomados directamente del fabricante, cuyas recomendaciones hay que tomar en cuenta antes de iniciar la prueba. El muestreo, por su parte, debe realizarse en un laboratorio para el mercado abierto. En tanto que el filtro se instala en el ducto de prueba de manera que la línea del centro coincida con la central del flujo de aire.
Procedimiento
1 Se determinan los parámetros para efectuar la prueba
- La velocidad de paso o flujo
- La presión diferencial final
2 Secuencia de prueba
- Resistencia contra flujo de aire del filtro limpio (∆P inicial)
- PSE del filtro limpio utilizando aerosol
- Cargar con polvo sintético (30 gramos) o hasta alcanzar un incremento de 0.04” PCA
- PSE del filtro utilizando aerosol
- Cargar con polvo sintético hasta alcanzar 25 % del ∆P final recomendado por el fabricante
- PSE del filtro utilizando Aerosol
- Cargar con polvo sintético hasta alcanzar 25 % del ∆P final recomendado por el fabricante
- PSE del filtro utilizando aerosol
- Cargar con polvo sintético hasta alcanzar 50 % del ∆P final recomendado por el fabricante
- PSE del filtro utilizando Aerosol
- Cargar con polvo sintético hasta alcanzar 75 % del ∆P final recomendado por el fabricante
- PSE del filtro utilizando Aerosol
- Cargar con polvo sintético hasta alcanzar el ∆P final recomendado por el fabricante
Durante estos procedimientos hay que estar atentos a las mediciones de eficiencia (con el contador), las cuales se toman durante el proceso de carga en función de la saturación. Posteriormente, se elaboran las gráficas correspondientes para cada etapa, empezando por el filtro limpio.
Reporte de prueba
Una vez realizada la prueba, se elabora un reporte con la siguiente información:
- Nombre del Laboratorio
- Operador y fecha de la prueba
- Información del contador de partículas
- Datos del filtro según el fabricante
- De dónde se obtuvo la muestra
- Condiciones en que se realizó la prueba
- Eficiencia promedio
- Clasificación del filtro
El ASHRAE 52.2 ofrece grandes beneficios, pues facilita la comprensión de cómo trabaja un filtro y su desempeño, utiliza tecnología confiable para clasificar un filtro, pero, sobre todo, la prueba está bajo control de manera permanente, gracias al uso del aerosol. Con esto, se garantiza que el aire que corre en una habitación y que respiran los usuarios del lugar no contenga agentes contaminantes que perjudiquen su salud o dañen la operación de los equipos.
—–
Fernando Bonilla
Director en Ingeniería para Ambientes Limpios (INPAL). Cuenta con experiencia en filtros de aire y Calidad Ambiental Interior (CAI), así como una especialidad para todo tipo de instalaciones, desde hospitales hasta la industria petrolera.