Conoce el funcionamiento, la versatilidad y los beneficios ambientales de los equipos de recuperación de calor, una misma tecnología para cubrir de modo eficiente y sostenible la demanda de frío/calor hasta para cuatro aplicaciones distintas: chiller + calderas + heat pump + simultáneo. Lo anterior en un escenario de calentamiento global y frente a la exigencia de reducir el uso de combustibles fósiles para generar calor
Pedro Machain / Imágenes: cortesía de EcoChillers
Los sistemas de recuperación de calor son aquellos que aprovechan el rechazo de calor de procesos, lo que se denomina como energy waste o desperdicio de energía, para proporcionar refrigeración y, por lo tanto, calentamiento al mismo tiempo. Esta tecnología fue desarrollada para mejorar la sustentabilidad y el ahorro de energía en diferentes procesos de producción en industrias como las de alimentos, farmacéutica, plástico, automotriz, metal mecánica, hospitalaria, etcétera.
En toda la industria el aumento de los precios de energía es un desafío importante. Los días de la era de la energía barata terminaron y la eficiencia energética se está convirtiendo en un factor de éxito crucial. Actualmente, se estima que el potencial de ahorro energético en edificaciones industriales es tres veces la capacidad de generación de energía nuclear, es decir, equivalente a 2.6 teravatios por hora.
La buena noticia es que en la mayoría de los procesos industriales existe un considerable potencial de ahorro energético sin explotar. Un informe de la Agencia Internacional de la Energía afirma que las plantas industriales de todo el mundo utilizan un 50 por ciento más de energía de la necesaria. Al cambiar a una tecnología con mayor eficiencia energética las empresas pueden lograr grandes ahorros y reducir de forma significativa su impacto ambiental.
En el caso del consumo de energía para satisfacer la demanda de frío/calor de los procesos industriales las fuentes pueden ser dos: a) los combustibles fósiles, y b) la electricidad para motores y aplicaciones específicas.
A su vez, los flujos de calor pueden ser de dos tipos:
1. Los flujos de energía sin aprovechamiento del exceso de calor.
• Combustible.
• Generación de calor (quemadores, calentadores).
• Proceso.
• Enfriamiento.
• Ambiente.
2. Los flujos de energía con aprovechamiento del exceso de calor.
• Combustible.
• Generación de calor + calor recuperado.
• Proceso + calor recuperado.
• Recuperación de calor.
• Enfriamiento.
• Ambiente.
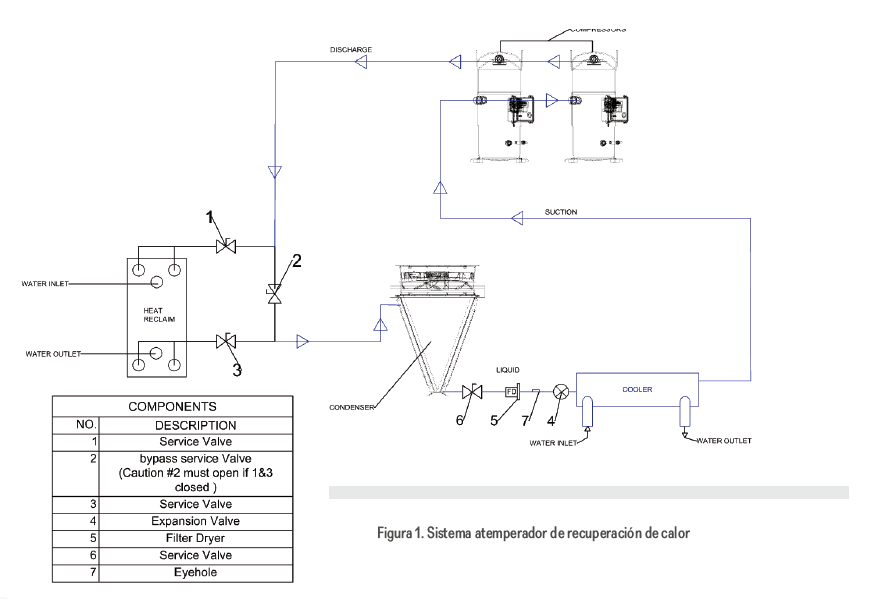
Figura 1. Sistema atemperador de recuperación de calor
¿Cómo funciona la recuperación de calor?
El propósito de la recuperación de calor es justamente aprovechar los flujos de energía del exceso de calor. En otras palabras, se basa en reutilizar la energía térmica sobrante o de deshecho generado en procesos industriales, así como la energía calorífica generada por el ciclo de refrigeración de los equipos de aire acondicionado y refrigeración (RAC).
El potencial de ahorro de energía y costes está estrechamente relacionado con el “flujo de calor” en la mayoría de los casos. La idea básica detrás de la recuperación de calor residual es tratar de recuperar la máxima cantidad de calor generada en la planta o instalación RAC de un edificio para reutilizarlo tanto como sea posible, en lugar de simplemente liberarlo al aire o a un río cercano. Es decir, en lugar de sólo desperdiciarlo, el calor es transformado para poner en marcha otros procesos de enfriamiento y calefacción.
Adicionalmente, el calor recuperado puede aprovecharse en combinación con calor de desperdicio para producir:
• Agua caliente.
• Agua fría.
• Agua destilada.
• Tratamiento de aguas negras.
Los procesos industriales de generación de calor generalmente tienen lugar en calderas de vapor, calentadores eléctricos y/o hornos infrarrojos. En ambos casos, la recuperación del calor residual a menudo reduce la necesidad de vapor en una planta. En consecuencia, el consumo de combustible de la caldera disminuye, al igual que las emisiones de gases de efecto invernadero (GEI) y la carga en el sistema de refrigeración. El calor recuperado también se puede utilizar para precalentar la alimentación de la caldera, lo que reduce el consumo de combustible. También el consumo de combustible de un horno de infrarrojos se puede reducir utilizando el calor residual del enfriador para precalentar la alimentación del calentador. Una vez más, esto reduce las facturas de combustible, la carga del sistema de refrigeración y las emisiones de GEI.
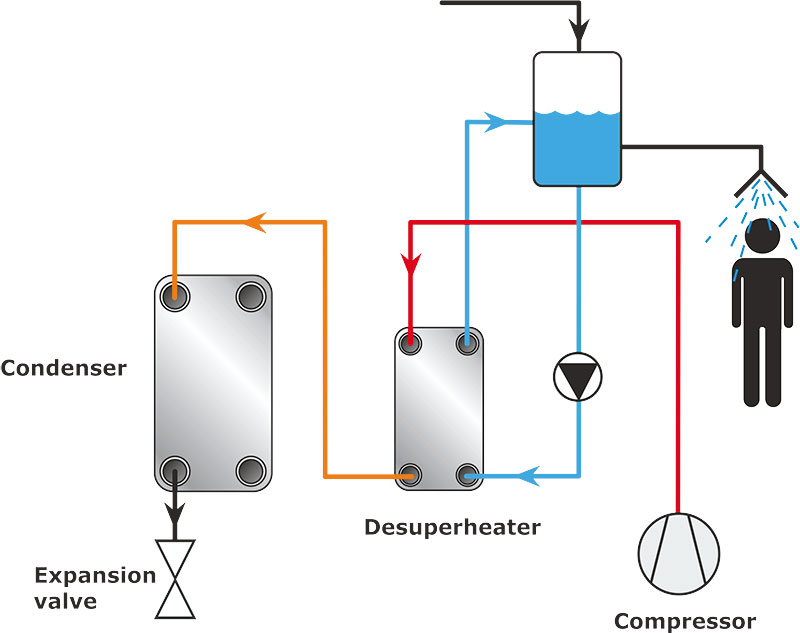
Figura 2. Diseño esquemático de un sistema de recuperación de calor para proporcionar agua caliente para duchas.
Tipos de intercambiadores de calor
El componente clave en los sistemas de recuperación de calor residual son los intercambiadores de placas. Hoy en día, además, están los Shell Box intercambiadores de coraza con tubería de titanio, resistentes al agua clorada, las aguas negras y grises. Estos dispositivos son diseñados para proporcionar una transferencia de calor eficiente entre dos fluidos. Cada diseño depende del fabricante que las produzca; sin embargo, todos tienen algo en común: buscar alcanzar un equilibrio entre calidad, precio y tiempo de entrega. Sus aplicaciones van desde refrigeración, aire acondicionado, calefacción, evaporación hasta condensación, por lo que existen diferentes tipos.
Los intercambiadores de calor de placas soldadas (BPHE) y de microplacas soldadas (MPHE) son ampliamente utilizados en chillers. Son compatibles con diversos fluidos y aunque sus dimensiones son reducidas, poseen una gran área de transferencia. Los BPHE se pueden utilizar como condensadores, evaporadores y condensadores de circuito dual, además de contar con un flujo tridimensional. En cambio, los MPHE son fabricados con aluminio y ofrecen un flujo bidimensional con una velocidad más uniforme, lo cual mejora considerablemente la transferencia de calor.
El diseño de los BPHE consiste en una serie de placas delgadas y corrugadas de acero inoxidable, soldadas con cobre o níquel, mientras que los MPHE, son más ligeros y operan con menor cantidad de refrigerante, pero alcanzan una mayor transferencia de calor por metro cuadrado. Por lo tanto, representan mayor rendimiento para el sistema RAC, utilizando menos energía.
La rentabilidad de una inversión depende en gran medida de la eficiencia de los intercambiadores de calor y de los costes del ciclo de vida asociados (adquisición, mantenimiento, etcétera). Estos factores varían considerablemente entre las diferentes tecnologías de intercambiadores de calor. Si bien actualmente los intercambiadores de calor compactos de titanio o de acero inoxidable son muy comunes, en las industrias de procesos siguen dominando los intercambiadores de carcasa y tubos.
Los intercambiadores de calor compactos tienen muchos beneficios sobre los de carcasa y tubos:
• Eficiencia de transferencia de calor hasta cinco veces mayor.
• Menores costes tanto de inversión inicial como de mantenimiento.
• Mucho más pequeño en tamaño.
La Figura 3 muestra el nivel de recuperación de calor en función de la constante inicial. El rendimiento de los intercambiadores de calor compactos es hasta un 25 por ciento mayor que el de los de carcasa y tubos a un coste comparable. En definitiva, se trata de una forma sencilla de aumentar la eficiencia energética en plantas industriales. Las inversiones suelen ser muy rentables y los plazos de amortización suelen ser inferiores a un año.
Una solución 4 en 1
En la actualidad, es posible encontrar sistemas de enfriamiento que utilizan la tecnología de recuperación de calor completa (full heat recovery) para ofrecer cuatro soluciones en una: chiller enfriado por aire/agua. + boilers + calderas + bomba de calor agua/agua.
Ahora bien, ¿a dónde se envía este excedente calorífico recuperado? En edificios comerciales, por ejemplo, un lugar ideal para redireccionar el calor de rechazo son los sistemas de calefacción y calderas en hoteles, hospitales, laboratorios y edificios comerciales.
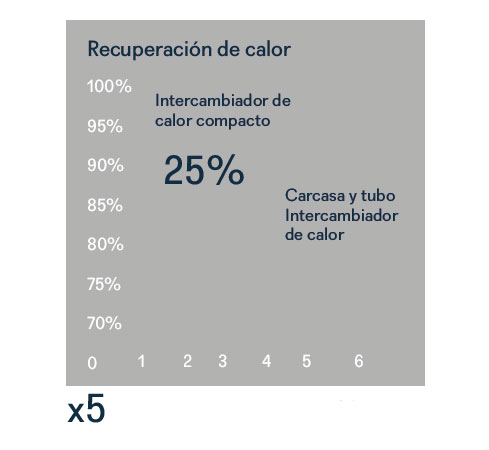
Figura 3. Rendimiento de los intercambiadores de calor compactos versus los de carcarsa y tubos.
Algunos de los beneficios de los equipos cuatro en uno de recuperación de calor son:
1. Ahorro de combustible para calentar los servicios de agua caliente sanitaria (baños, duchas).
2. Aprovechamiento del calor para generar calefacción habitaciones.
3. Reducción o eliminación del consumo de agua en la torre de enfriamiento evaporativo.
4. Reducción de los costos de inversión de capital en los sistemas de calentadores.
5. Reducción de las emisiones de gases de efecto invernadero.
6. Reducción del mantenimiento y uso de las torres de enfriamiento.
7. Reducción del consumo de energía para el tratamiento del aire, al ser utilizado en los serpentines de recalentamiento de unidades manejadoras para controlar o reducir la humedad
El proceso de recuperación es teóricamente igual para los sistemas que funcionan enfriados por aire o por agua. Se debe disponer de calor de rechazo y de un fluido receptor de este producto, donde la fuente que posee mayor energía “cederá” parte de su energía al receptor, el cual posee una menor cantidad de energía que incrementará al estar en contacto con la fuente a través del intercambiador de calor empleado. Las válvulas de cuatro vías que permiten tener agua fría y caliente al mismo tiempo, sin que se tenga que hacer un ciclo inverso.
En síntesis, la solución de recuperación de calor completa es una alternativa sostenible y eficiente para satisfacer las necesidades de calefacción y enfriamiento al tiempo de incrementar la eficiencia energética en plantas de edificios de todo tipo. En la mayoría de los casos, la inversión de estos equipos se paga en menos de un año. Su instrumentación, además, disminuye hasta en un 100 ciento por ciento el consumo de combustibles fósiles, por lo que representan una mejor opción que las calderas tradicionales. Lo anterior reduce el impacto ambiental de las industrias y mejora el desempeño de las instalaciones RAC en edificaciones de todo tipo.
Pedro Machain
EcochillersInc Ingeniero Industrial por del Valle de Atemajac (UNIVA), con más de 35 años de experiencia en la industria HVACR. Fundador y CEO de Ecochillers Corporation.