Conoce los conceptos clave, las herramientas básicas, el desempeño energético y los requerimientos de seguridad para llevar a cabo un buen manejo de hidrocarburos inflamables, una alternativa natural y sustentable para mejorar la eficiencia energética de los sistemas RAC
Gildardo Yañez
Para poder reducir realmente las emisiones de gases de efecto invernadero (GEI) de la industria de la refrigeración y el aire acondicionado (RAC) es necesario transitar hacia el uso de refrigerantes sustentables y, de igual forma, incrementar la eficiencia energética de los sistemas. Al hablar del impacto ambiental del sector hay que considerar dos tipos de emisiones: las directas que son causadas por las fugas de refrigerante, y las indirectas, que son producto de las emisiones de dióxido de carbono equivalente (CO2eq) que se producen al generar energía eléctrica con combustibles fósiles.
En este escenario, el uso de refrigerantes hidrocarburos (HC) inflamables ayudará a reducir las emisiones indirectas, ya que representan sustancias naturales de bajo potencial de calentamiento global (PCG) y que, además, requieren mucho menos consumo de energía para enfriar.
El PCG mide los kilogramos equivalentes de CO2 que tienen los refrigerantes al ser liberados en la atmósfera. Así, es posible comprobar que 1 kg de emisión de R-404A es igual a 3,920 kg de dióxido de carbono a la atmósfera. En cambio, si la emisión es de 1 Kg de R-290 (propano) se reduce a un valor menor de 3 kg. Una hidrofluoroolefina como el R-1234yf da un valor inferior a 1, comparado contra el R-410A que da un total de 2,088 kg. No en vano, el R-410A está siendo sustituido por refrigerantes de bajo PCG como el R-32 o el R-454B y en un futuro cercano por el R-290 en minisplits.
La importancia de transitar hacia refrigerantes más amigables con el medioambiente radica también en la eficiencia energética. El efecto de refrigeración del R-22 o el R-410A va de entre 73.5 y 75.2 BTU/Ib. En cambio, los refrigerantes como el R-290 y el R-600a tienen un efecto de 130.7 y 127.4 BTU/Ib, respectivamente. Es decir, duplican la potencia del efecto de refrigeración, por lo que reducen también el consumo de energía, no sólo el PCG.
¿Qué son los HC?
Los HC son gases hidrocarburos licuados del petróleo a presión. Cuando pasan del estado líquido al gaseoso súbitamente se expanden mucho más de lo acostumbrado que otros fluidos. Por ejemplo, un litro de R-290 genera en fase líquida 273.8 litros de gas a una temperatura de 21 °C, es decir, que un litro pesa 500 gramos (g), aproximadamente.
El uso de HC no está exento de riesgos. Uno de los principales a considerar es su venteo o liberación al medioambiente, ya que crecen exponencialmente en tamaño. Tan sólo un litro de R-290 puede generar 273 litros de vapor de propano que, al mezclarse con el aire, puede llegar a formar hasta 12,475.45 litros de mezcla inflamable. Lo anterior podría ser el detonante de un incidente de inflamabilidad, si no se procuran las condiciones adecuadas de seguridad.
Las técnicas aprobadas para trabajar con HC se pueden encontrar en el Estándar Competencia Laboral EC-1389, diseñado para trabajar con hidrocarburos inflamables como el R-600a y el R-290. Dicho estándar certifica a los técnicos en el manejo de HC. Actualmente, los refrigeradores domésticos ya vienen con el R-600a y en la refrigeración comercial se utiliza el R-290, por lo que cada vez hay más equipos que utilizan HC como refrigerante alternativo al uso del R-134a.
Los HC no son inflamables por sí mismos. De hecho, bajo las cargas permitidas en la actualidad en México no es probable que se alcancen los niveles de concentración necesarios para generar una ignición. En junio del 2024, para el aire acondicionado en la Unión Europea se permitirán cargas de hasta 988 g y para la refrigeración comercial la carga máxima permitida será de 500 g. Dentro de unos años no sería extraño que México igualara las normativas europeas o norteamericanas, pasando de 150 a 500 gramos en equipos autocontenidos con puertas y 500 gramos en equipos sin puertas. Por eso es muy importante que los técnicos se familiaricen con el tema y, de este modo, ser capaces de afrontar los retos futuros.
Definiciones clave
El principal aliado a la hora de trabajar con estos refrigerantes es la información. Los datos y las definiciones precisas ayudan a distinguir los refrigerantes hidrocarburos de los sintéticos inflamables. Uno de los conceptos base es el llamado “calor de combustión”, que se define como la medida de la cantidad de calor que se libera cuando se quema una sustancia, en este caso, un refrigerante.
Otra definición clave es la “energía mínima de ignición” (MIE o minimum ignition energy), que es la energía de chispa eléctrica mínima en milijoules (mJ) requerida para encender una mezcla de gas/aire inflamable. Para esta medida se toma como referencia la chispa de una bujía de alto voltaje, que produce entre 20 y 30 mJ de energía de ignición.
Los refrigerantes de clase A2L tienen un calor de combustión mucho menor que los refrigerantes A3. Además, la mayoría de los A2L son difíciles de encender debido a su elevado MIE. De acuerdo con datos del Instituto de Aire Acondicionado, Calefacción y Refrigeración (AHRI, por sus siglas en inglés), es muy poco probable que el calor de artículos domésticos como taladros, secadores de pelo o calentadores logren encender estos refrigerantes, además de que la ignición también requiere de niveles muy elevados de concentración en la zona.
También está el “límite inferior de inflamabilidad” (LFL o lower flammability limit). Este término refiere a la concentración mínima de una sustancia inflamable que es capaz de encenderse cuando hay una mezcla suficiente del aire con la sustancia. Este índice siempre se expresa en un porcentaje de refrigerante por volumen. La inflamabilidad de los refrigerantes se determina mediante la prueba de inflamabilidad ASTM E-681, referida en el estándar ASHRAE 34/ISO 817.
A su vez, la “velocidad de incineración” de un gas combustible es la velocidad con la que un frente de llama se propaga en relación con el gas no quemado por delante de la llama. Los refrigerantes A2L tienen una velocidad de combustión de 10 cm/s o menos, por lo que es menos probable que mantengan la combustión después de que se haya eliminado la fuente de ignición inicial. Refrigerantes como el R-32 o el R- 454B tienen una velocidad de incineración 6.7 y 5.2 cm/s, respectivamente. Mientras que los refrigerantes A3, como el propano R-290 y el isobutano R-600a, tienen una velocidad de incineración superior a 10 cm/s. El primero de 46 cm/s y el segundo de 41 cm/s, por lo que es observable una diferencia significativa.
Respecto al calor de combustión (el calor que generan en caso de ignición), el propano y el isobutano alcanzan índices de 19,905 y 19,200 BTU/Ib. No obstante, para que lleguen a un punto de autoignición se necesitan temperaturas muy elevadas; por ejemplo, para el propano se requieren 455 °C. De igual modo, en la parte de energía mínima de ignición el propano y el isobutano requieren de muy poca energía, pero los refrigerantes A2L necesitan de 30 a 10,000 mJ, dependiendo el caso. En síntesis, la principal diferencia entre los refrigerantes A2L y los A3 es que los segundos liberan mucho más calor y su velocidad de incineración es mucho más rápida.
Herramientas base
Otra definición importante al manipular los HC es el “límite de concentración de refrigerante”, que se utiliza para determinar la concentración máxima permitida en un espacio ocupado. Al trabajar con equipos diseñados para hidrocarburos es necesario utilizar ciertas herramientas críticas para prevenir que se rebase el límite de concentración:
• Báscula gramera para refrigerantes inflamables.
• Manifold aprobado para el uso de refrigerantes A3 y A2L.
• Ventilador de especificación ATEX para el control de áreas explosivas. Esta herramienta ayuda a diluir el gas e impedir la concentración en caso de un escape de refrigerante en la zona de trabajo.
• Probador de polaridad de contactos de 127 VCA.
• La bomba de vacío certificada para refrigerantes A2L y A3. Ésta debe tener un cable con una longitud de 3 m y un motor a prueba de chispa.
• Detector de explosividad que se coloca en la parte baja de los refrigeradores para medir si presentan alguna fuga de refrigerante.
• Extintor que sea capaz de apagar el fuego en el volumen de la zona de trabajo.
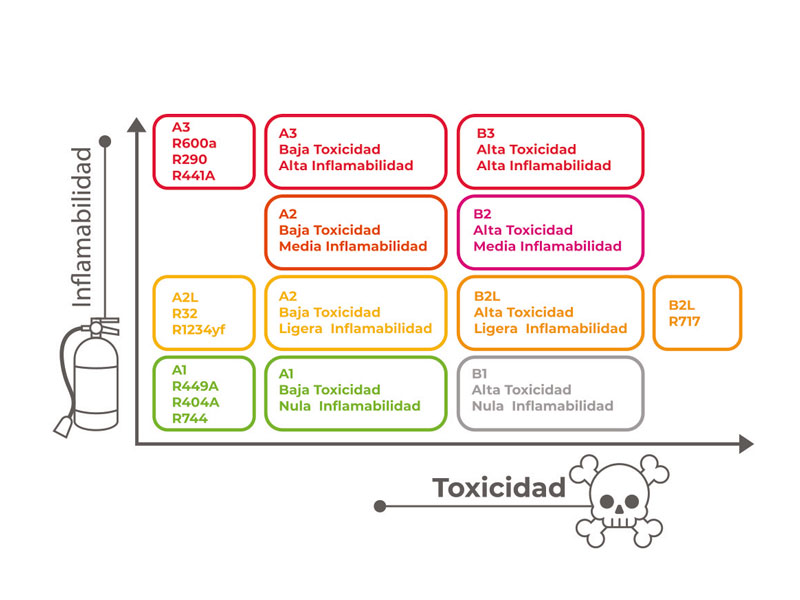
Figura 1.
El Estándar 34/ISO/817 de ASHRAE define 8 grupos de seguridad.
De igual modo, el equipo debe estar aterrizado, es decir, tener una conexión a tierra certificada bajo la NOM-022-STPS en donde se conecte la recuperadora y el tanque recuperador para que el técnico pueda trabajar con la seguridad de que no se generará una descarga electrostática.
Control de inflamabilidad
Los prestadores de servicio técnico deben conocer la diferencia entre los refrigerantes A1, A2, A2L y A3, listados en el Estándar 34 de ASHRAE, principalmente en lo referente a sus índices de inflamabilidad y toxicidad. La mayoría suele trabajar con refrigerantes A1, pero eventualmente éstos irán desapareciendo y la industria RAC se moverá hacia los A2L y, después, hacia los A3, que requieren aún más medidas de seguridad.
Una de las principales diferencias son los valores de inflamabilidad de cada clasificación de refrigerantes. Los A3 liberan un calor de combustión mayor a 19,000 BTU/Ib; los A2L tienen valores menores a ese rango; mientras que para los A1 la inflamabilidad es nula.
Los refrigerantes A2L requieren de una gran concentración en volumen y una fuente grande de ignición para lograr la combustión, a diferencia de los A3 que requieren de poco volumen y de poca energía para ignicionar. Para evaluar esto se ocupa el método de prueba de inflamabilidad ASTM E-681, en donde se genera una llama que debe encenderse en un ángulo de 90°. Dependiendo de la extensión de la llama desde el centro hasta los 90°, se clasifica el nivel de inflamabilidad del refrigerante.
Ninguno de los refrigerantes formados en la letra A es tóxico, pero sí cambian su nivel de inflamabilidad, pues a medida que disminuye el potencial de calentamiento global los refrigerantes se hacen más inflamables. También existen mezclas zeotrópicas para refrigeración como el R-451A y el R-451B, dos alternativas al R-134a, que en un futuro podrían competir con refrigerantes naturales como el propano. A la fecha, ASHRAE ha aprobado varias de estas mezclas, mismas que ya se encuentran disponibles en los catálogos de los fabricantes en México. No obstante, todas están sujetas a un tiempo de reducción de 30 años, periodo establecido por los diferentes organismos internacionales en el que se verá qué opciones funcionan mejor.
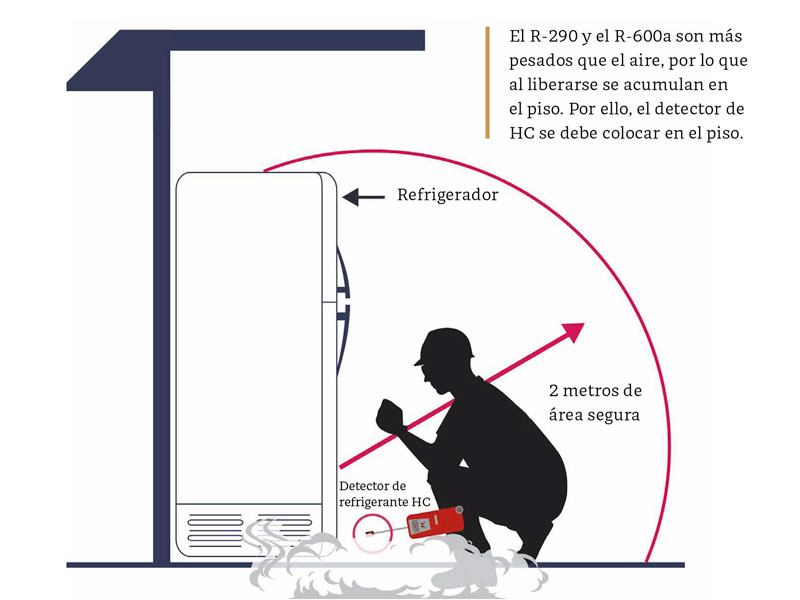
Figura 2.
Área segura para refrigerador.
Los refrigerantes hidrocarburos como el R-290, cuya vida atmosférica es de 14 días, no reaccionan con ningún componente del sistema de refrigeración y cuando se liberan al medioambiente no generan smog. Lo anterior debido a que se descomponen en CO2 y vapor de agua. El primero se absorbe en la fotosíntesis vegetal y el H2O se integra al ciclo del agua.
Indicaciones de seguridad
Los HC deben estar claramente etiquetados para identificar el tipo de refrigerante e indicar que el contenido del cilindro es inflamable. Los pictogramas mínimos que deben tener son:
• La advertencia de seguridad para el uso del refrigerante.
• La nomenclatura del refrigerante y el número C.A.S.
• La marca registrada del fabricante.
• La cantidad del producto en peso neto.
Estos datos son importantes para que el técnico pueda verificar que el refrigerante que va a cargar es seguro y confiable para el sistema. También es necesario llenar la hoja de seguridad del refrigerante, asegurarse de cumplir con toda la normativa estipulada, utilizar herramientas críticas aprobadas para el refrigerante A3 y conocer las técnicas de recuperación.
Los técnicos, por su parte, deben considerar las llamadas “zonas temporales inflamables”, es decir, las regiones en las que se prevé que se produzcan al menos algunas emisiones de refrigerante durante los procedimientos normales de trabajo como la recuperación, la carga, etcétera. Siempre se debe considerar el tamaño estipulado de la zona de trabajo, que puede llegar a medir dos metros. Nunca se debe hacer el vacío dentro del espacio confinado, sino que la bomba debe tener una manguera que dé al exterior para que todo el vapor que se extraiga del sistema de refrigeración se quede fuera.
Recuperación activa y pasiva
Para realizar la recuperación pasiva de refrigerante se utiliza una técnica aprobada para equipos con cargas menores a los 500 g, en la que se utiliza la diferencia de presión y de temperatura entre el tanque recuperador y el sistema de refrigeración. El tanque recuperador debe tener un vacío previo de 1,000 micrones y contar con hielo.
Otra recomendación es que la recuperación del refrigerante se lleve a cabo con válvulas rápidas y con pinzas pinch-off, pues así lo indica el Manual de la Semarnat y el Estándar de Competencia Laboral.
Para realizar la recuperación de manera activa sólo se debe ocupar la válvula piercing del lado de alta y luego poner a funcionar el equipo. El tanque de recuperación debe estar en hielo y con los micrones de vacío necesarios para después arrancar el compresor. Es así como el refrigerante del lado en alta presión se traslada al tanque recuperador, se condensa y se recupera hasta en una carga máxima de 500 g.
Venteo de refrigerantes HC
Para ejecutar el venteo de HC se deben tomar ciertas consideraciones. En primer lugar, el venteo se tiene que controlar con el manifold y se debe usar el detector de gases hidrocarburos para cuidar que no se eleven los niveles de concentración. En segundo, la manguera de purga deberá apuntar al exterior de la zona de trabajo y tener dos metros de altura.
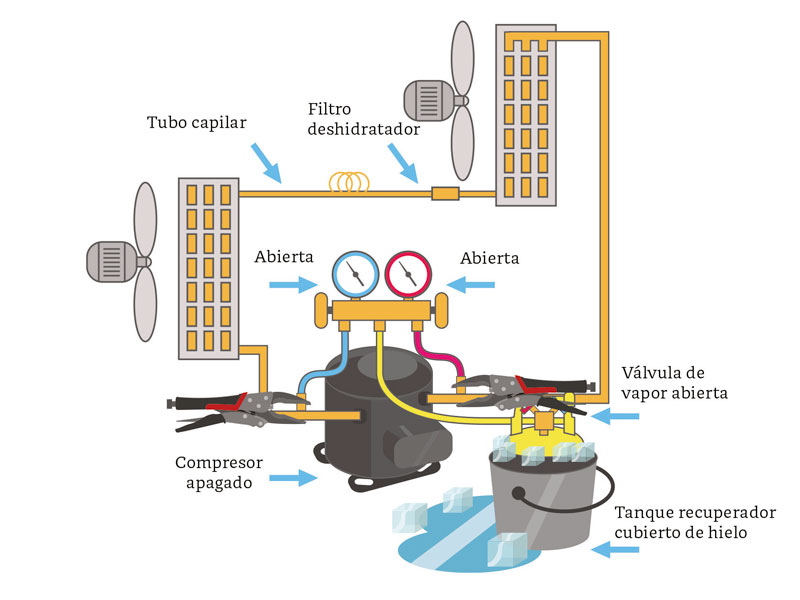
Figura 3. Recuperación sin recuperadora (recuperación pasiva del refrigerante).
Una vez que el refrigerante salió con la bomba de vacío se baja la presión del sistema hasta llegar a 2 psig para remover los residuos de HC. Nunca se debe ventear libremente el refrigerante, sino que éste debe pasar a través del tanque recuperador como medida de seguridad, ya sea una carga máxima de 500 g o una carga menor. Además, el proceso de recuperación también ayuda a separar el aceite que puede viajar con el vapor hidrocarburo.
En la recuperación de refrigerantes inflamables es fundamental evitar la transferencia de gases no condensables como el aire al cilindro de recuperación, puesto que el oxígeno crea una mezcla combustible crítica a presiones más altas con los refrigerantes HC, que puede provocar un accidente. Además, se debe tener cuidado con el equipo eléctrico que se usa en la recuperación; por ejemplo, el cilindro debe tener el mismo potencial eléctrico que la unidad de recuperación (unión equipotencial) para evitar una descarga electrostática.
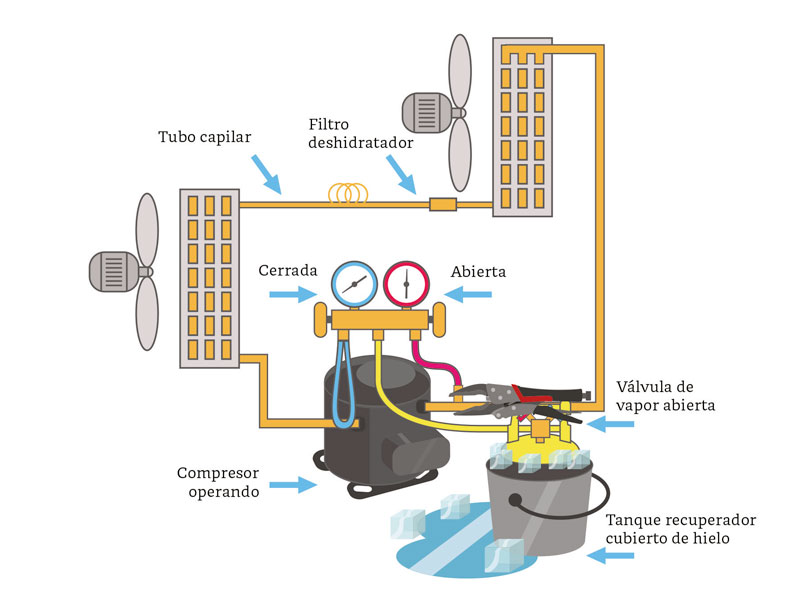
Figura 4. Recuperación de refrigerante acelerada activa.
Los tanques deben ser exclusivos para refrigerante HC y cada cinco años se les debe hacer la prueba de presión hidrostática, o bien, una prueba de presión obligatoria para tener la seguridad de que el tanque sigue en buenas condiciones. El cilindro siempre tendrá que ser pesado para verificar que esté vacío, pues la presión no es un indicador preciso de la cantidad de refrigerante que resta. Para poder determinar la capacidad del cilindro, se debe multiplicar la capacidad de agua (WC) por la gravedad específica (SG) del refrigerante a una temperatura de 25 °C (77 °F). Esto es así porque los HC líquidos ocupan más del doble del volumen dentro de un tanque.
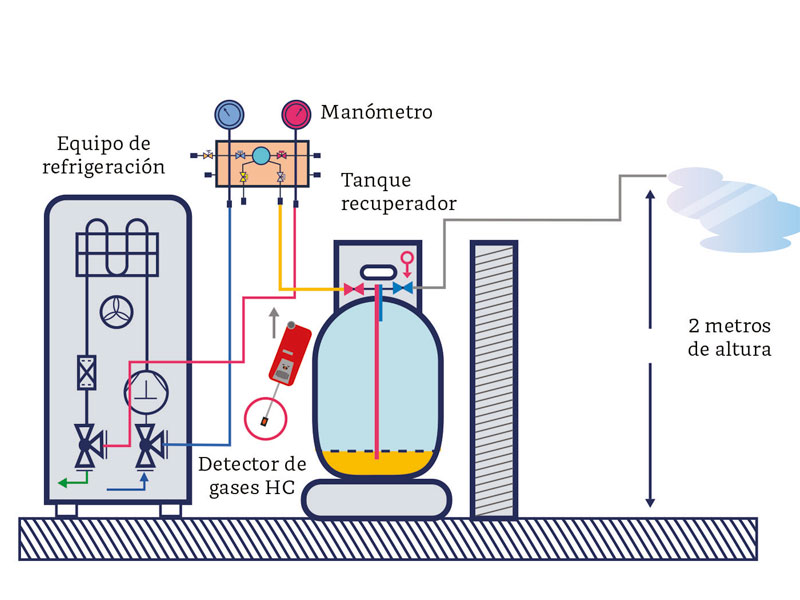
Figura 5. Conexión para el venteo seguro de refrigerante HC.
Cabe destacar que la guía para la eliminación de refrigerantes dañinos para el medioambiente como el R-12 es el Protocolo de Montreal. Hoy en día, además, se impulsa la reducción del R-134a o el R-410A, dos sustancias que están siendo sustituidas por HC en varias aplicaciones. Junto con los avances en normatividad y los nuevos sistemas de alta eficiencia energética, es muy probable que para el 2025 el uso de refrigerantes inflamables sintéticos en México sea más seguro y común de lo esperado, incluso en minisplits.
Gildardo Yañez
BLOG: https://www.gildardoyañez.com Ingeniero Industrial Electricista, con una Maestría en Administración. Cuenta con más de 40 años de experiencia profesional, 30 de éstos en la refrigeración. A lo largo de su trayectoria ha capacitado a cientos de técnicos en México y América Latina. Actualmente, se desempeña como Gerente de Capacitación Técnica en BOHN de México.